Examples of Process monitoring and Control
All Sensors can be monitored Remotely and Alarmed where existing equipment has Modbus RS485 or 4-20mA Output.
All these individual processes can be connected together to one dashboard.
Chemicals available for all systems mentioned. See chemistry page.
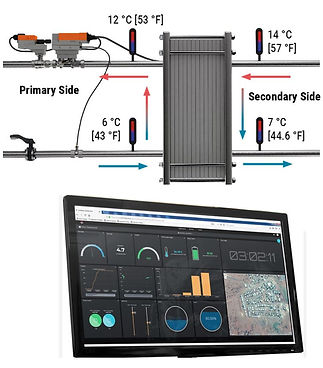
Heat Exchanger Condition Monitoring.
Online heat exchanger condition monitoring involves continuous assessment of key parameters like temperature, pressure, and fluid flow to ensure optimal performance. Regular inspections and data analysis help identify potential issues, such as fouling or leaks, allowing for timely maintenance and preventing efficiency loss or equipment failure in industrial processes. Early alarming and data will ensure proactive targeted maintenance.

Reverse Osmosis Plant Monitoring.
Reverse osmosis plant monitoring ensures efficient water purification by regularly assessing key parameters like pressure, flow rates, and water quality. Real-time data analysis helps detect issues such as membrane fouling or scaling, allowing for timely corrective action. This proactive approach ensures consistent and high-quality water production in reverse osmosis systems used for desalination, water treatment, and various industrial applications. Including critical water and chemical tank level monitoring to ensure ongoing preventative actions is adhered to.
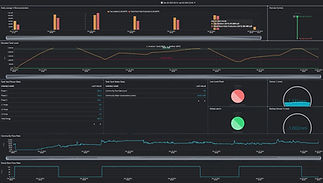
Storage (Chemical/Water) Tank level Monitoring
Ensure you are prepared and maintain the minimum levels at all time. Allowing for pre-set minimum re order levels to be adhered by and removing the human error. Running our of chemicals for maintenance and general operation can have big financial implications from penalties, charges plant failure and production continuity.

Corrosion and Scale Formation Monitoring
Corrosion and scale formation monitoring is the continuous assessment of metal degradation and mineral deposition in industrial systems. Sensors and analytics track factors like pH, conductivity, and real time metal corrosion rates. This proactive approach helps identify potential issues, prevent equipment damage, and optimize maintenance schedules, ensuring the longevity and efficiency of infrastructure in processes such as water treatment and treatment of mill and ash lines. Scale and Corrosion Coupons will also be utilised for physical/visual verification of results.

Total Plant Water Balance, usage and leak detection
Total plant water balance involves tracking water inputs, usage, and outputs to ensure efficient water management. Advanced monitoring systems detect abnormal usage patterns and identify leaks promptly. This data-driven approach aids in optimizing water consumption, minimizing waste, and addressing issues swiftly, contributing to sustainable practices and resource conservation in industrial settings such as manufacturing plants, mining or water treatment facilities.

Water Treatment online control and Automation.
Water treatment online control and automation involve real-time monitoring and adjustment of key parameters like TDS (Automated Blow down, pH, ORP, free chlorine, temperature, and inhibitor proportional dosing. Automated systems maintain optimal conditions by continuously analyzing data and adjusting chemical dosages. This ensures efficient treatment processes, water quality compliance, and proactive measures to prevent issues, enhancing overall system performance and longevity and lifespan of equipment.
​
Pre treatment for all systems on case by case scenario to be designed and implemented according to system requirements.